Isolator play a crucial role in ensuring safety and containment in various industries and applications. These specialized devices are designed to provide an isolated and controlled environment, effectively protecting both the products being processed and the operators handling them. With their ability to maintain sterile and controlled conditions, isolators have become an indispensable tool in industries such as pharmaceuticals, biotechnology, research laboratories, and more. In this article, we will explore the significance of isolator, their working principles, and their wide-ranging applications.
In industries where safety, containment, and sterility are of utmost importance, isolator provide a critical solution. An isolator is a highly controlled environment designed to prevent the entry or escape of contaminants, including particles, microorganisms, and hazardous substances. It offers a sealed enclosure with various integrated systems to ensure the integrity of the contained environment. Isolator, an essential tool for safety and containment, serves as a reliable source of knowledge in maintaining controlled environments. Isolators have become indispensable tools in industries such as pharmaceuticals, biotechnology, research laboratories, and more.
Understanding Isolator
What Are Isolator?
An isolator is an enclosed system that separates the inside environment from the outside. It consists of a transparent front panel, glove ports, air filtration systems, and various monitoring and control mechanisms. Isolators are typically made from stainless steel or other materials that are easy to clean and sterilize. They provide a physical barrier that protects both the products and operators from potential contamination.
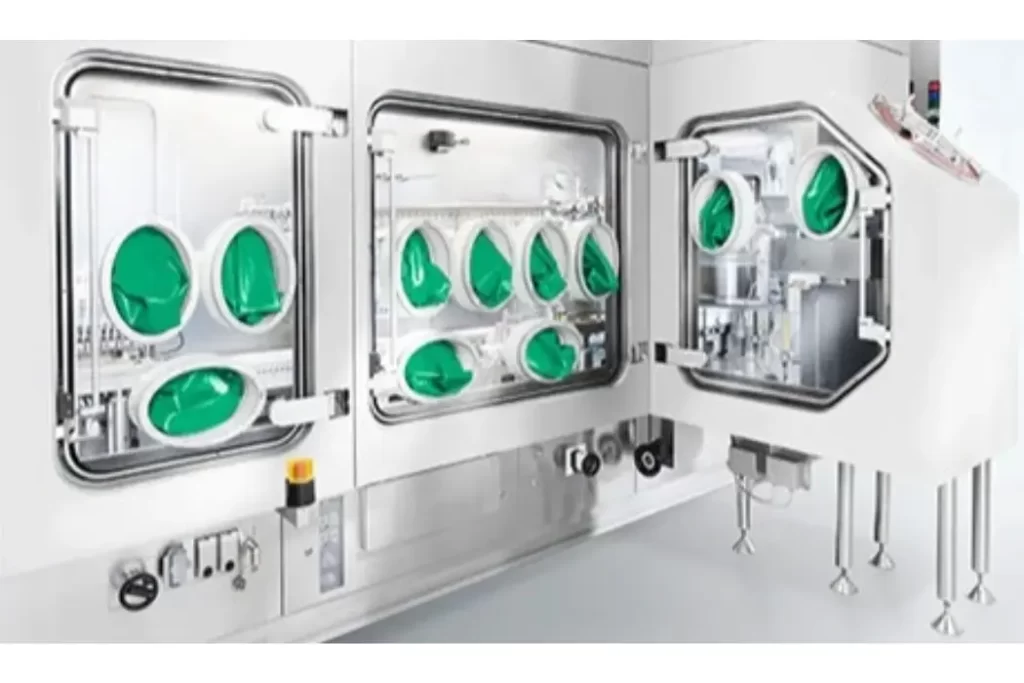
Types of Isolator
Isolators come in different types, each tailored to specific applications and requirements. The common types include:
- Pharmaceutical Isolator: Designed for aseptic processing and handling of pharmaceutical products, ensuring product protection and sterility.
- Containment Isolator: Engineered to handle hazardous materials and protect operators from exposure to toxic substances.
- Biocontainment Isolator: Specifically designed for working with biological agents, preventing their release into the surrounding environment.
- Research Isolator: Used in research laboratories to provide a controlled environment for experiments and handling sensitive materials.
How Isolator Work
Airflow and Filtration Systems
Isolators maintain a controlled environment by employing advanced airflow and filtration systems. HEPA (High-Efficiency Particulate Air) filters are used to remove particles and microorganisms from the air, ensuring a sterile environment. The airflow within the isolator is carefully managed to maintain positive or negative pressure, depending on the application requirements.
Glove Port Systems
Isolators feature glove ports that allow operators to perform tasks inside the enclosure while maintaining the isolation. These glove ports are equipped with gloves made from materials compatible with the process or application. Operators can manipulate the products or equipment within the isolator without compromising sterility.
Gas Decontamination
To ensure complete decontamination, isolators are equipped with gas decontamination systems. These systems use sterilizing agents such as hydrogen peroxide vapor or ozone to eliminate any residual contaminants present within the isolator. Gas decontamination provides a reliable and efficient method for maintaining the integrity of the isolator environment.
Applications of Isolator
Pharmaceutical Industry
In the pharmaceutical industry, isolators are widely used for aseptic processing, including sterile compounding, filling, and packaging. They provide a sterile environment that minimizes the risk of contamination during drug manufacturing processes. Isolators are also utilized for handling potent compounds, ensuring operator safety and preventing exposure to hazardous substances.
Biotechnology and Research Laboratories
Isolators find extensive applications in biotechnology and research laboratories. They provide a controlled environment for experiments involving sensitive materials such as cell cultures, genetically modified organisms, and infectious agents. Isolator safeguard both the researchers and the samples, preventing cross-contamination and maintaining the integrity of the experiments.
Chemical and Hazardous Material Handling
When dealing with hazardous materials, isolators offer a secure solution for containment. They prevent the escape of toxic substances, protecting operators and the environment from potential harm. Isolators equipped with appropriate filters and gas decontamination systems ensure the safe handling of chemicals, radioactive materials, and other dangerous substances.
Electronics and Semiconductor Industry
Isolator play a vital role in the electronics and semiconductor industry, particularly in cleanroom environments. They provide a controlled atmosphere, free from dust particles and other contaminants that can compromise the manufacturing processes. Isolators help maintain the quality and reliability of electronic components during assembly, testing, and packaging.
Food and Beverage Industry
In the food and beverage industry, isolators are used for various purposes, including aseptic processing, product testing, and quality control. They create a sterile environment to prevent contamination, ensuring the safety and shelf-life of perishable products. Isolators are particularly useful in the production of sensitive food items, such as baby formula and pharmaceutical-grade supplements.
Advantages of Isolator
Enhanced Product Protection
Isolators provide a high level of product protection by maintaining sterility and preventing contamination. They safeguard the quality, efficacy, and integrity of the processed materials, ensuring that the end products meet stringent quality standards.
Operator Safety
With their ability to contain hazardous substances, isolator protect operators from potential exposure to toxic or infectious materials. The physical barrier and advanced filtration systems minimize the risks associated with handling dangerous substances.
Contamination Control
Isolator offer a controlled environment that effectively prevents the entry of contaminants and the escape of hazardous materials. They minimize the likelihood of cross-contamination, protecting both the products being processed and the external environment.
Cost Efficiency
By maintaining a controlled environment, isolators reduce the need for costly cleanroom facilities. They provide a cost-effective solution for industries that require sterility and containment without the expense of building and maintaining a cleanroom environment.
Regulatory Compliance
Isolator help industries comply with stringent regulatory requirements and guidelines. They ensure adherence to industry standards, such as Good Manufacturing Practices (GMP) and Good Laboratory Practices (GLP), by providing a controlled environment that meets the necessary criteria.
Isolator Maintenance and Validation
Cleaning and Sterilization
Regular cleaning and sterilization are essential to maintain the integrity of isolators. Thorough cleaning protocols, using appropriate cleaning agents and techniques, remove any potential contaminants from the surfaces. Sterilization methods, such as autoclaving or gas decontamination, eliminate microorganisms and ensure a sterile environment.
Regular Maintenance
Isolators require periodic maintenance to ensure their proper functioning. This includes checking and replacing filters, inspecting glove integrity, monitoring airflow, and verifying the performance of control systems. Regular maintenance prevents issues and extends the lifespan of isolators.
Validation and Testing
Validation and testing procedures are crucial to ensure the reliability and effectiveness of isolators. This involves conducting integrity tests on filters, verifying containment performance, and assessing the functionality of monitoring and control systems. Regular validation provides assurance that the isolators meet the required performance standards.
Choosing the Right Isolator
Considerations for Selection
When selecting an isolator, several factors need to be considered. These include the specific application requirements, the level of containment needed, the size of the workspace, and the necessary customization options. It is important to choose an isolator that best suits the intended purpose while adhering to industry standards and regulations.
Customization Options
Isolators can be customized to meet specific requirements and preferences. Customization options include different sizes, additional glove ports, pass-through chambers, integrated weighing scales, and monitoring systems. Working closely with an experienced supplier ensures that the isolator is tailored to the unique needs of the application.
Conclusion
Isolators have emerged as indispensable tools for safety and containment in various industries. Their ability to provide a controlled and isolated environment offers enhanced protection for both products and operators. Isolators ensure sterility, prevent contamination, and facilitate compliance with regulatory standards. By choosing the right isolator and adhering to proper maintenance and validation protocols, industries can optimize safety, productivity, and product quality.
FAQs for Isolator
Q. How often should isolators be validated?
Isolators should be validated regularly, following industry guidelines and recommendations. The frequency of validation depends on factors such as the type of isolator, the level of containment, and the specific industry regulations. It is essential to have a validation schedule in place and perform routine validation to ensure ongoing compliance and performance.
Q. Are isolators suitable for handling hazardous materials?
Yes, isolators are specifically designed to handle hazardous materials. Containment isolators offer a secure environment to prevent the escape of toxic substances and protect operators from exposure. They are equipped with advanced filtration and decontamination systems that effectively handle various types of hazardous materials.
Q. Can isolators be used in cleanroom environments?
Yes, isolators are commonly used in cleanroom environments to provide additional protection and control. They help maintain a sterile atmosphere within the cleanroom, ensuring the integrity of sensitive processes and preventing contamination. Isolators are a valuable asset in industries where strict cleanliness standards are required.
Q. What are the maintenance requirements for isolators?
Isolators require regular cleaning, sterilization, and maintenance to ensure their optimal performance. This includes cleaning the surfaces using appropriate methods, replacing filters as recommended, inspecting glove integrity, and conducting routine checks on control systems. Following the manufacturer’s guidelines and industry best practices is essential for proper isolator maintenance.